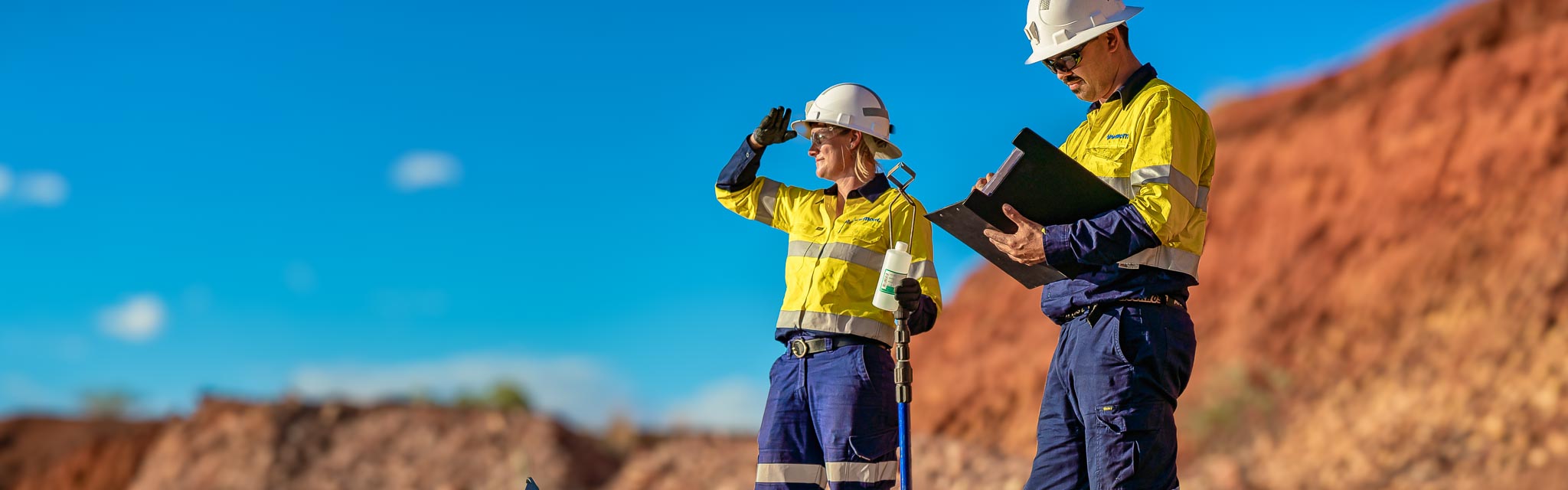
Unearth Your Potential
Join Newmont Today!
Heading
About Newmont
Newmont is the industry's leading gold and copper business and a producer of zinc, lead, and silver. The company's world-class portfolio of assets, prospects and talent is anchored in favorable mining jurisdictions in Africa, Australia, Latin America & Caribbean, North America, and Papua New Guinea. Newmont is the only gold producer listed in the S&P 500 Index and is widely recognized for its principled environmental, social, and governance practices. The company is an industry leader in value creation, supported by robust safety standards, superior execution, and technical expertise. Join us and help us deliver on our purpose to create value and improve lives through sustainable and responsible mining.
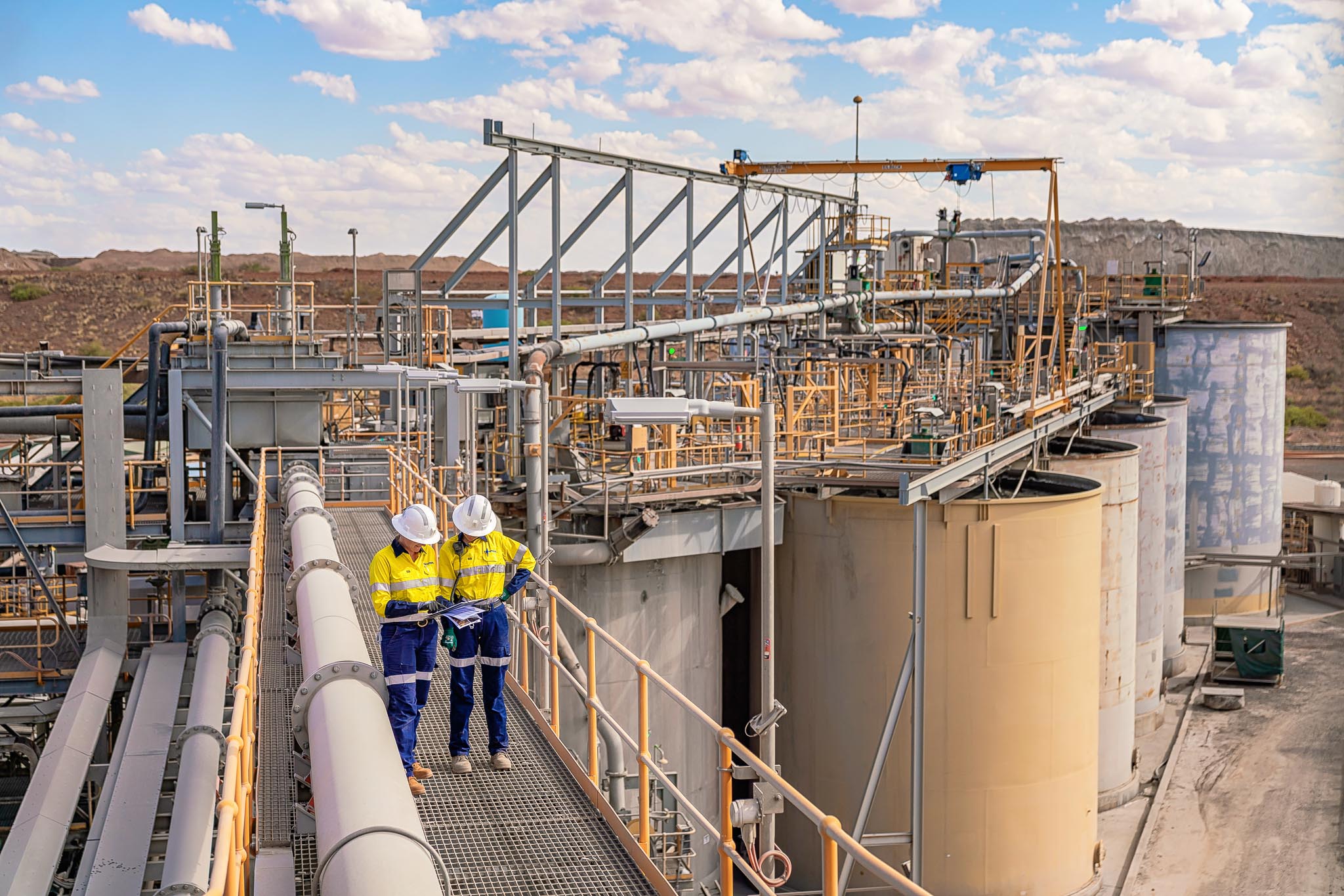
Heading
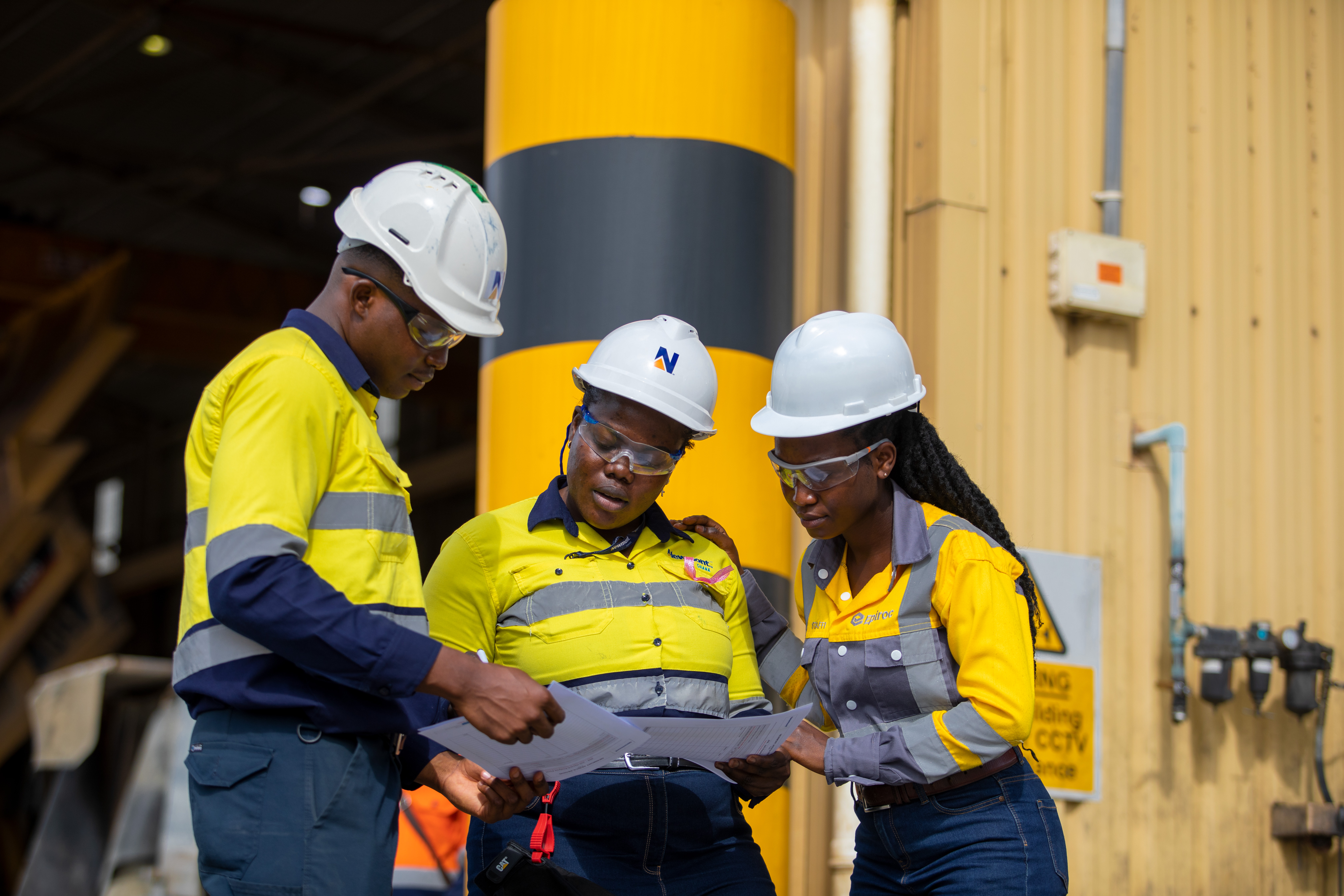
Life At Newmont
It is our strong-held belief that we maintain a competitive advantage through our people with industry leading engagement, leadership, and commitment to inclusion, and responsibility are engrained in our culture, and impact each action we take. That is why we strive to establish a culture where everyone belongs, thrives, and is valued. Join us on our journey of innovation and purpose, where together, we're shaping a sustainable and inclusive future for all.
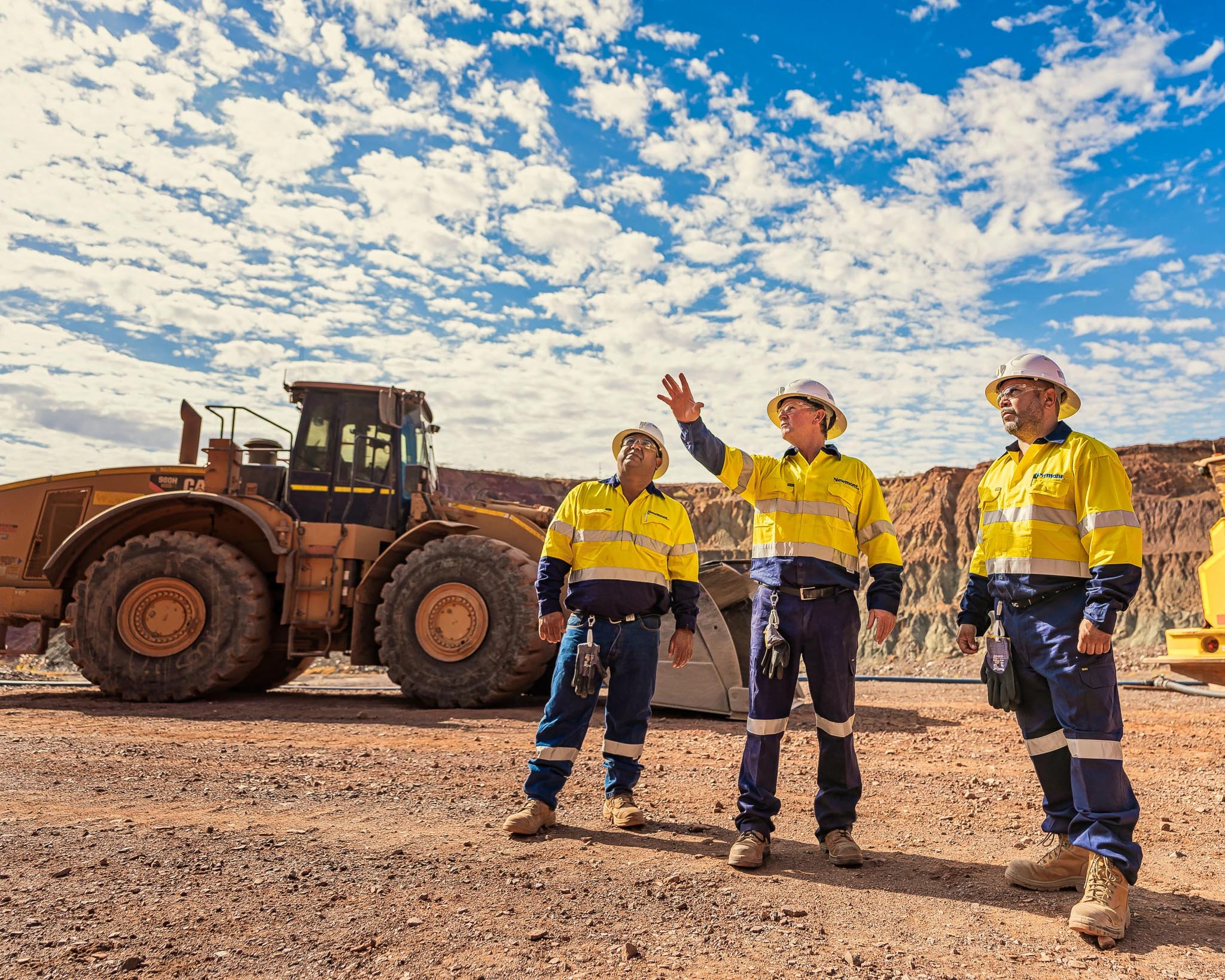
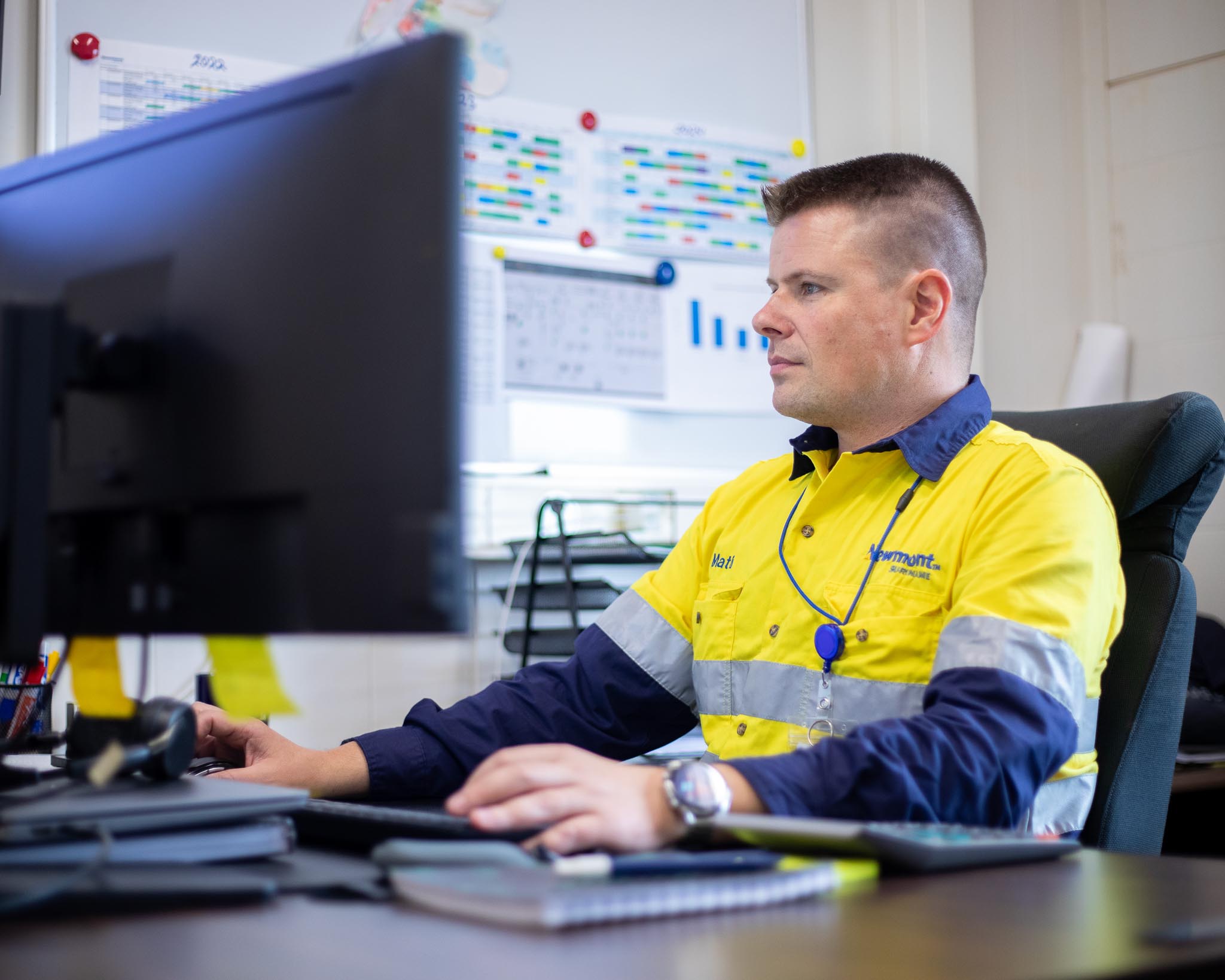
Lorem Ipsum has been the industry's standard dummy text
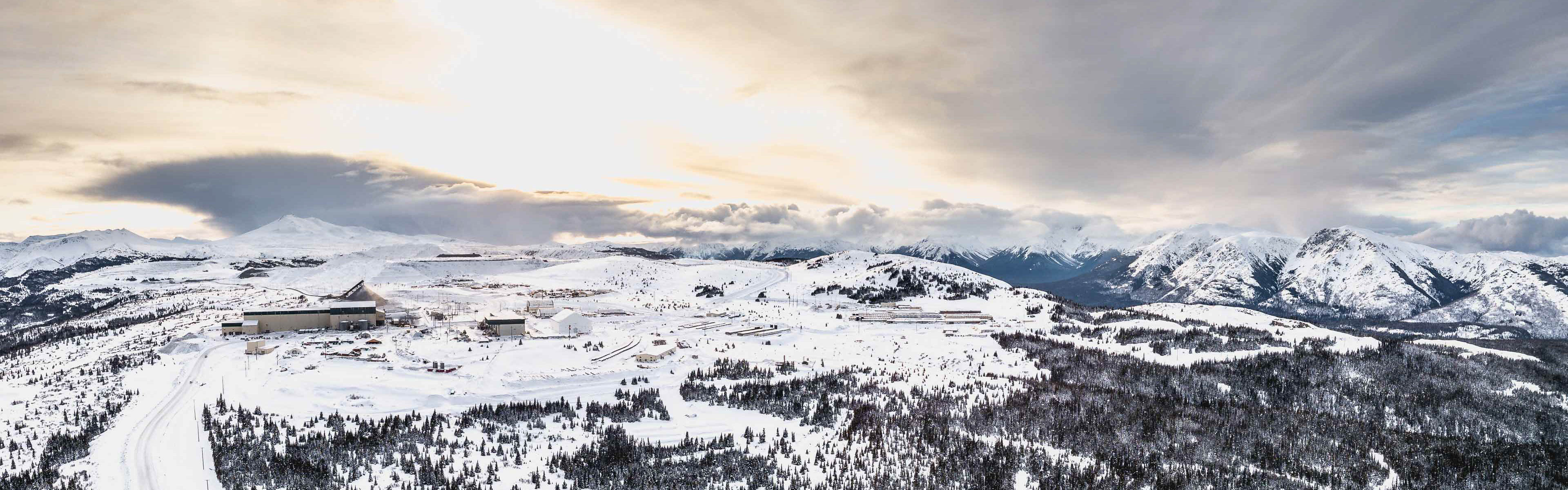